Collaborative Robots: What Are They and What Are Their Benefits?
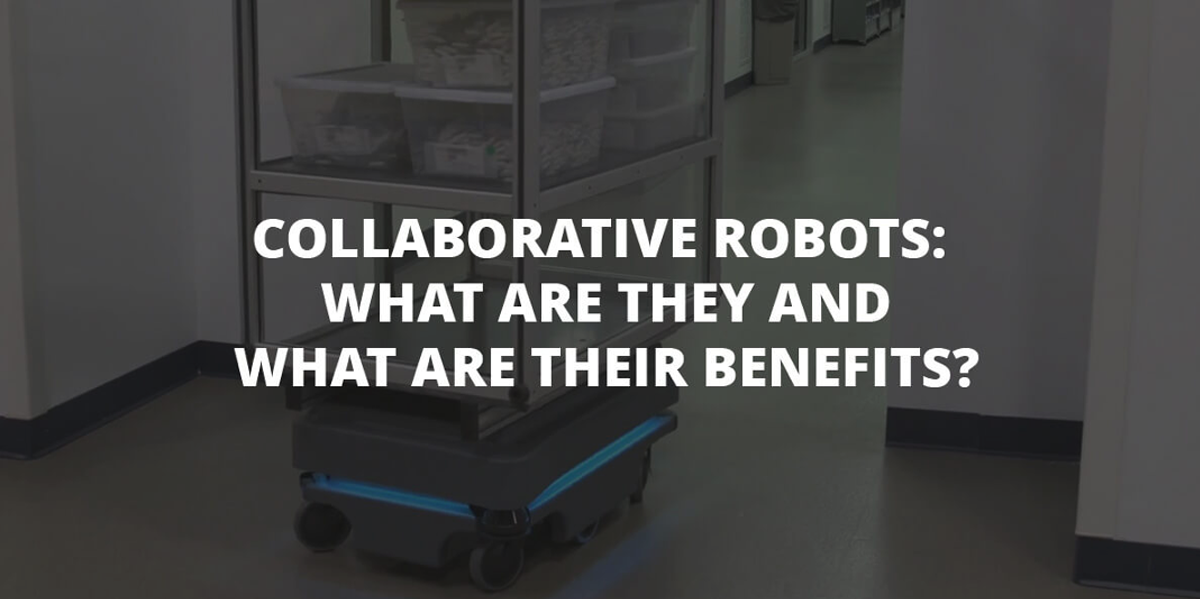
Automation is a growing trend in industrial facilities worldwide. However, there is also a growing concern that robots will take over human jobs. Collaborative robots work by augmenting the human workforce, enabling small to medium-sized businesses (SMBs) to boost productivity while maintaining their existing staff.
What Are Collaborative Robots?
Collaborative robots, sometimes called cobots, are built to work safely with humans. In a collaborative industrial workspace, the cobot performs repetitive manual tasks while the human workers focus on more thought-intensive responsibilities.
With more businesses of all sizes incorporating cobots in their processes, the market has a projected compound annual growth rate of 32%
over the next decade. The primary drivers of this growth include:- Ongoing labor shortages across almost all industries
- The need for resiliency against sudden disruptions like COVID-19
- Companies see cobots as a way to stay competitive
- Higher demand for fast ROI and increased profitability
Various industries have adopted cobots, including equipment manufacturing, food and beverage and even the service industry.
Collaborative vs. Traditional Robots: What Is the Difference?
Cobots differ significantly from their larger industrial counterparts. Here are a few of the essential differences.
Cobots
Cobots are best suited for low-volume manufacturing applications where flexibility is key. They can adapt easily to changing work requirements, so manufacturers that produce multiple different products are most likely to benefit.
The primary goal of cobot design is safety. They have rounded edges and sensors to prevent unwanted contact with human workers. If a collision does happen, the cobot's safety protocols kick in, and it automatically shuts down.
They're also more user-friendly than traditional robots, so workers with minimal experience can learn to program them for new applications.
Traditional Robots
Traditional robots, often called "non-collaborative" or "industrial" robots, are best suited for large-scale mass production — applications where companies need to produce big batches of a product with minimal variations.
These robots work at incredibly high speeds and often have much larger payloads than cobots, which is why they can pose a risk to nearby human workers. Facilities must install machine guarding and protective fencing around traditional robots to ensure the safety of their workers.
The Benefits of Collaborative Robots
Implementing cobots helps you gain an edge over your competition. Here are some of the top benefits:
- Flexibility: Cobots are easy to program for different tasks, making them highly versatile. They're also a great way of future-proofing your facility against the possibility of another global crisis like COVID-19.
- Cost-effectiveness: Because setup and programming are so simple, you don't need to pay for in-depth training sessions and integration resources. And because safety is built into their design, you can save on safety equipment like fencing or machine guarding.
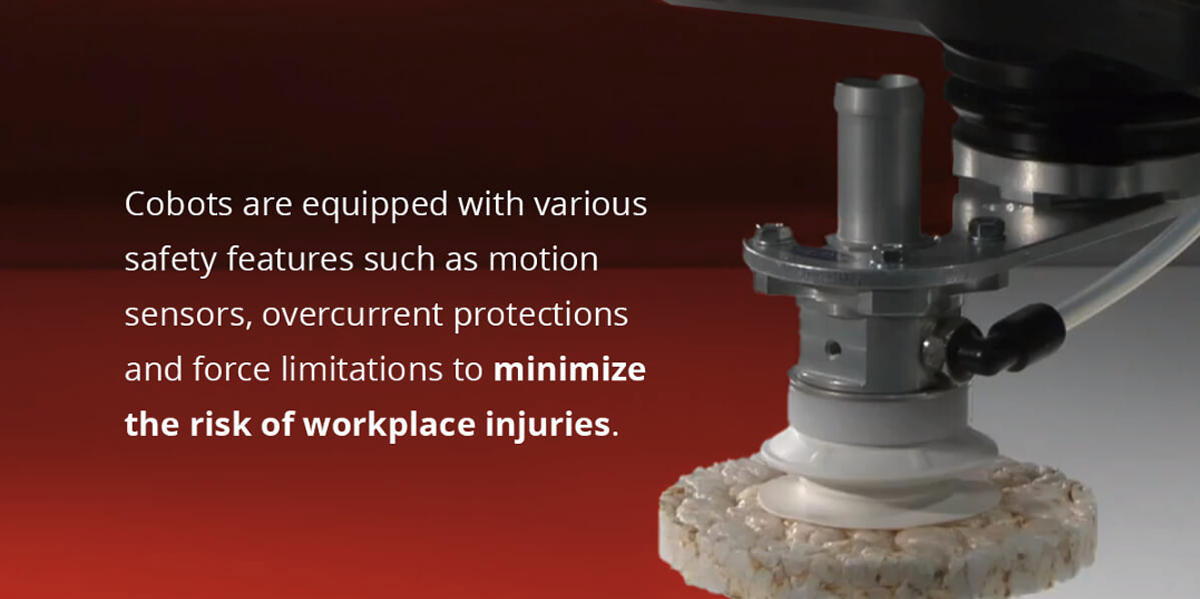
- Safety: Cobots are equipped with various safety features such as motion sensors, overcurrent protections and force limitations to minimize the risk of workplace injuries.
- Rapid ROI: You can install and set up most cobots in only a few hours, so they can get to work right away. In some cases, you could even make a return on your investment in only a few months.
Our Collaborative Robots
At Gibson Engineering, we provide customized solutions for the following cobot brands.
Universal Robots
Universal Robots offers five robotic arm solutions for a wide range of applications. Their robots are lightweight and easy to move, making them ideal for facilities with limited space. Additionally, they're highly adaptable — when your needs change, you can easily reprogram them to maintain high productivity.
MiR Mobile Industrial Robots
MiR's user-friendly, flexible robots help companies increase internal logistics efficiency by automating and optimizing material handling and transportation. MiR offers eight advanced autonomous robots that deliver rapid ROI — many customers make a return on investment in under a year.
Our Accessories
We partner with some of the top cobot brands to create solutions that fit your facility's unique needs. Here's a quick overview of some of our top accessory vendors.
OnRobot
OnRobot's innovative end-of-arm grippers for cobots are compatible with several different robot brands, including Universal Robots. They're easy to install with user-friendly software, so you can get your cobot up and running quickly.
Asyril
Asyril produces three-axis vibratory feeding systems for cobots. The three-axis vibration technology enables the feeders to move parts gently as needed with little to no abrasion, making them ideal for even sensitive applications. Additionally, they're compatible with all part geometries and are easy to install and integrate.
Robotiq
Robotiq's flexible cobot grippers and accessories are simple and streamlined. They're designed for quick setup and implementation so you can return to work quickly.
ROEQ
ROEQ's purpose-built module solutions allow you to push the MiR Mobile Robots to their full potential. They're designed with various safety features, such as a patented locking system that ensures total visibility into your robots' locations. Further, they're easily interchangeable and highly versatile, making them ideal for facilities with changing requirements.
Schmalz
Schmalz produces a comprehensive range of end-of-arm vacuum accessories and grippers for cobots. They're ideal for applications such as pick-and-place, assembly and packaging, among many others.
SCHUNK
SCHUNK provides various grippers for various applications, including lab testing and material handling. Whatever your needs, SCHUNK's cobot accessories can help facilitate smooth robot-human interactions and fuel high productivity.
Specific Cobot Solutions
Robotiq's Palletizing Solution is an excellent example of how cobots can streamline work. This solution, which includes a UR10 robot, a pair of Robotiq arms and several accessories, enables you to automate palletization for maximum productivity.
It's also compatible with various other robot brands, allowing you to tailor the solution to your unique needs. Working with the team of expert engineers at Gibson Engineering can help you find the best accessories and parts to fully optimize your solution for the best results.
Gibson Robot Lab Solution
A robotic feasibility study gives us the real-world data necessary for finding the right solution for your application. Here's how the process works:
- 1. Define requirements: Include critical information like needed cycle time, intended payload, available working space and any environmental or safety concerns you may have.
- 2. Send us parts: Send our engineering team sample parts from your application and any required tooling or fixtures. This step helps us recreate your application requirements so we can get a comprehensive, accurate understanding of the process.
- 3. Proof of concept: A proof of concept test helps our engineers determine key details like the robot specifications and end-of-arm tooling needs. We'll also give you helpful feedback on the system's feasibility before moving on to the robot lab.
- 4. Review results: Once we have all the above data, we can recreate your application for physical testing in the Gibson Engineering Lab. We'll also provide additional notes and suggestions for accessories to optimize your investment.
For a more in-depth look at how the process might go for your facility, we invite you to contact us.
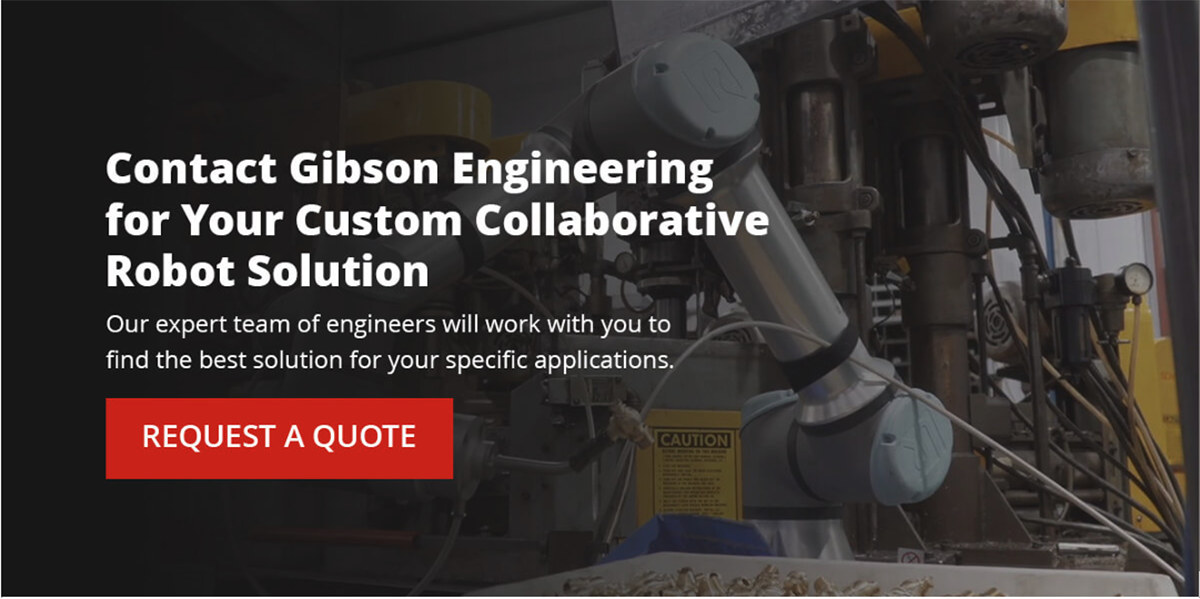
Contact Gibson Engineering for Your Custom Collaborative Robot Solution
If you're considering implementing cobots in your manufacturing facility, consider partnering with Gibson Engineering. Our expert team of engineers will work with you to find the best solution for your specific applications. Request a quote online today to get started.