What's the Difference Between Industrial and Collaborative Robots?
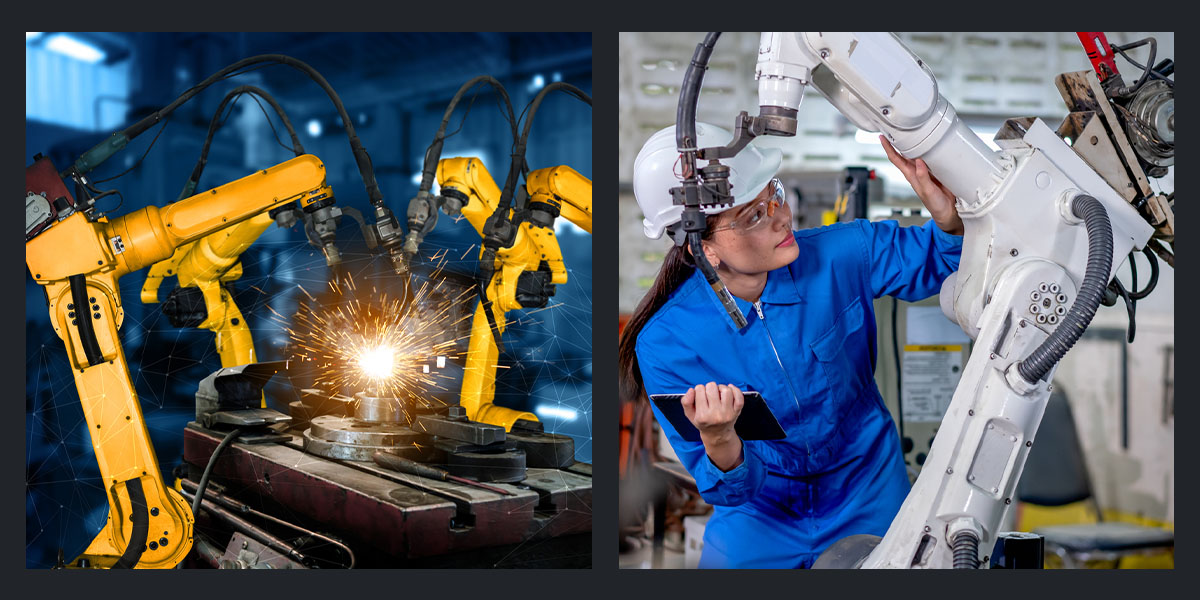
Industrial and collaborative robots revolutionize modern manufacturing and automation. They are redefining task management, enhancing productivity and boosting efficiency across industries. With sensors and mechanical precision, robots take on repetitive or hazardous tasks, increasing production line safety. Their adaptive capabilities also allow these machines to foster a dynamic and collaborative work environment alongside employees.
Industrial and collaborative robots can benefit your company in different ways. Understanding their key differences and applications can help you incorporate them into your business.
Differences Between Industrial and Collaborative Robots
Industrial or traditional robots and collaborative robots or cobots represent two distinct categories of automation technology. Their fundamental differences allow these machines to function as various automation solutions in several industries.
Industrial Robots
The stalwarts of manufacturing, these non-collaborative robots are built for large-scale mass production. They are single-task orientated, large, powerful and work at high speeds. They need protective fencing and machine guarding to keep workers safe. Traditional robots excel at heavy-duty and high-throughput tasks.
Collaborative Robots
Adapting to various work requirements easily, cobots are a good fit for manufacturing applications that demand flexibility. They are smaller, lighter and made to work alongside human counterparts, so safety is at the forefront of the collaborative robot's design. With rounded edges and sensors to help them navigate the workspace, they avoid collisions — if they do clash with objects or people around them, a safety protocol that shuts down the machine kicks in immediately.
The Functions of Industrial and Collaborative Robots
Cobots and industrial robots have similar functions, enabling organizations to automate manual processes. Choosing between the two depends on which will complement your business functions the most.
The Workhorses
Industrial robots are the workhorses of manufacturing as they perform a range of tasks with efficiency and precision. Their ability to perform tasks quickly, using high velocity, makes them well suited for applications like:
- Assembly: They can assemble intricate electronics or attach components in automotive manufacturing.
- Welding: With precision, these robots can create consistent and accurate welds for aerospace and automotive industry applications.
- Painting: These machines can ensure uniform and flawless paint applications in the consumer goods and automotive industries.
- Material handling: Streamline logistics and warehouse operations with the help of industrial robots. They can easily lift, transport and stack heavy payloads.
- Machine tending: They can be used in continuous production setups as these robots can load and unload parts.
The Assistants
The market size for collaborative robots is expected to expand at a compound annual growth rate (CAGR) of 32% by 2030. As they are designed to complement human efforts in the workplace, cobots can perform the following functions:
- Pick-and-place: These bots excel at repetitive tasks and are ideal for applications where they move items from one location to another.
- Quality inspection: Using cameras and sensors, cobots can perform rigid quality checks to ensure that products meet strict standards.
- Finishing: These robots can grind, polish and perform other finishing tasks to eliminate the risk of occupational hazards through repeated vibrational force on employees.
- Packaging: Cobots can shrink-wrap, move products and assemble boxes in a production line.
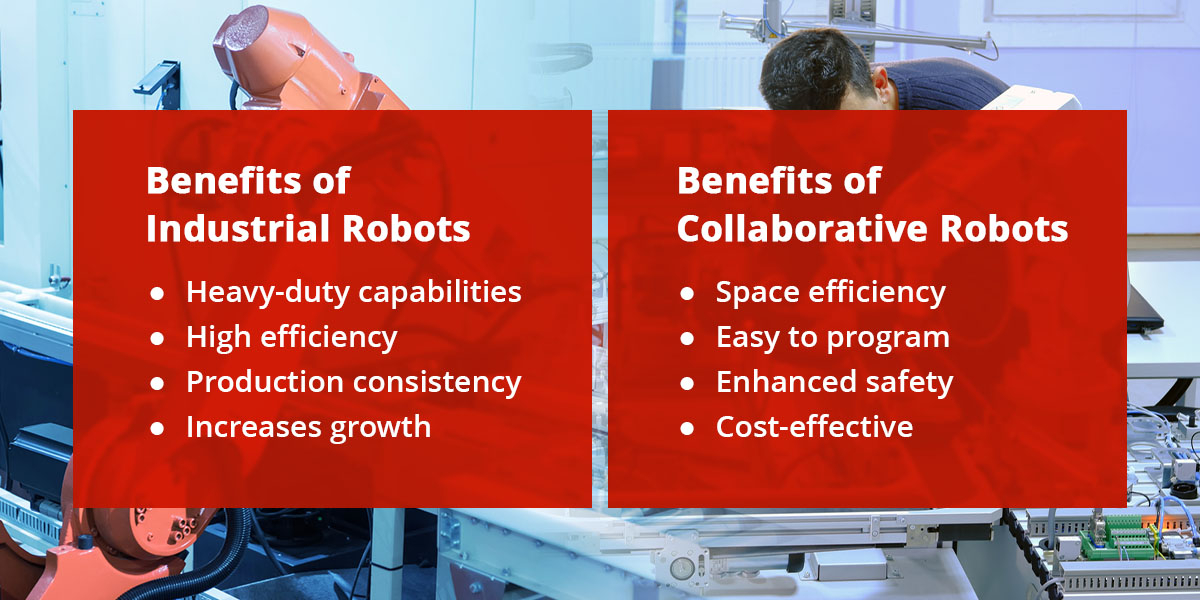
The Benefits of Industrial vs. Collaborative Robots
Industrial robots are a reliable solution for tedious, hazardous and repetitive tasks. New robot installation increased by 31% in 2021 compared to 2020, showcasing just how fast industries are adopting this technology. Robots allow employees to focus on areas where they can add the most value. Other benefits of these robots include:
- Heavy-duty capabilities: They can handle substantial weights and perform physically demanding tasks.
- High efficiency: Because they excel in repetitive and high-speed applications, they offer precision, contributing to better product quality.
- Production consistency: These robots maintain a steady level of performance, moving between tasks without delay and reducing variations in production output.
- Increases growth: Industrial robots offer scalability in their manufacturing capabilities, giving organizations room to expand production lines.
Collaborative robots are versatile thanks to their ease of programming. In addition to the ability to work 24-hour days,they take on intricate tasks and e can improve operational performance in various ways:
- Space efficiency: Because cobots are smaller and more lightweight, they are suitable for work in environments where space is limited.
- Easy to program: It is quick and easy to program these robots through mobile applications or user-friendly software. Many of these machines can also be set to specific positions manually, adding the benefit of a quick setup.
- Enhanced safety: These robots work with and alongside humans. They feature safety mechanisms and advanced sensors to lessen the risk of workplace accidents due to proximity.
- Cost-effective: Collaborative robots' purchase and maintenance costs are lower and feature less energy consumption due to their size.
Uses in Production
Each of these robots finds its niche in the world of automation, catering to distinct applications in various industries. Understanding their distinctions empowers industries to choose the ideal automation solution for their needs.
Industrial robots, offering power and precision, dominate manufacturing processes like welding, assembly and painting. They are crucial tools in the automotive industry, constructing vehicles with unwavering accuracy. In electronics manufacturing, they assemble tiny components on circuit boards. These traditional robots also find their place in logistics and warehousing, where they play a pivotal role in efficiently sorting, palletizing and packing inventory.
Collaborative robots shine in operations where they handle delicate or irregularly shaped items in pick-and-place operations. In health care, cobots often assist surgeons during surgeries, reducing human fatigue and adding precision to work. They are also a welcome addition to quality control and small-batch manufacturing, where their simple programming systems make them an invaluable tool to their human counterparts.
The Right Solution for Your Organization
By conducting a robotic feasibility study, engineers can use real-world data to find a robotic automation solution to enhance operational productivity, competitiveness and profitability. At Gibson Engineering, our engineers oversee a physical proof of concept test to help you understand capabilities and challenges related to your business needs.
We start by defining your requirements, like cycle time, payload and any environmental concerns you may have. Next, we sample parts from your application to help us better understand your application's process. We do the proof of concept, which comes with feedback on the system's feasibility, before offering results on the data. Here, you can expect suggestions and additional notes on how you can optimize your robotic investment.
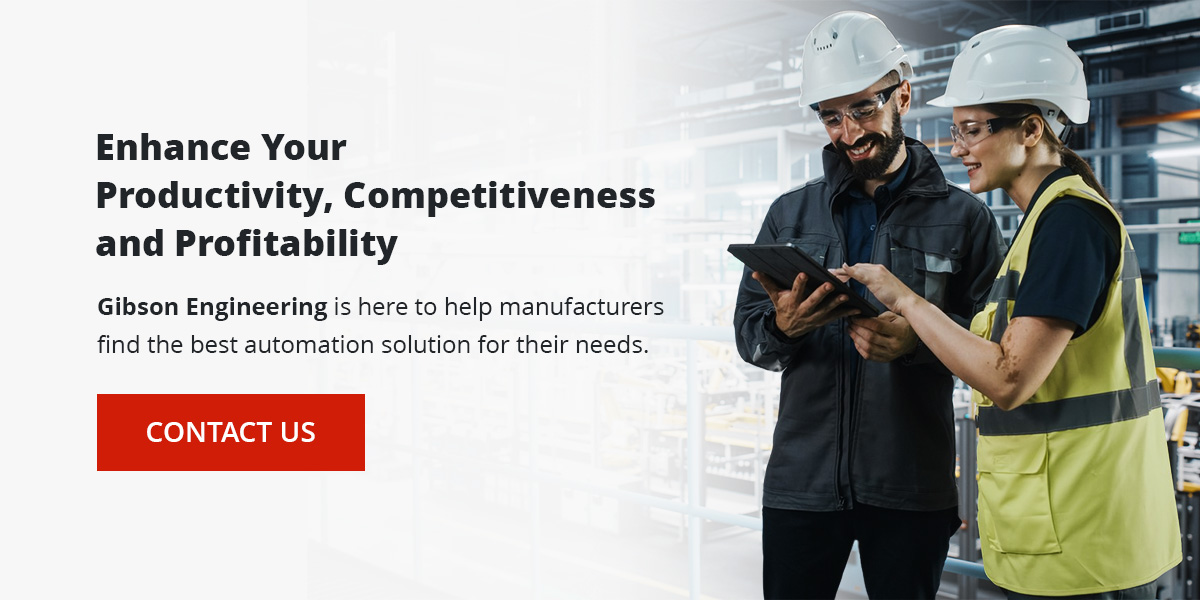
Enhance Your Productivity, Competitiveness and Profitability
Robots are the intelligent automation solution we have gained from Industry 4.0. As technology continues to advance, the synergy between industrial and collaborative robotic counterparts will also continue to revolutionize industries, offering even more production efficiency, high-quality product manufacturing and human-robot collaboration.
Gibson Engineering is here to help manufacturers find the best automation solution for their needs. Reach out to us for a robotic application evaluation or find out how we can help your organization increase productivity.